The Complex Manufacturing Process of Brake Pads
- Ultra Brake
- Jan 3
- 5 min read
Updated: Jan 5
Brake pads might seem like small and simple components, but their manufacturing process involves a meticulous and highly technical series of steps. These automotive brake pads play a critical role in ensuring vehicle safety by converting kinetic energy into thermal energy, bringing vehicles to a halt efficiently. Given their essential function, the production of brake pads requires precision engineering and extensive testing to meet stringent safety and performance standards. From the initial cutting of the steel backing plate to the formulation of friction materials, followed by rigorous brake pad testing standards under extreme conditions such as high temperatures, corrosion resistance, and real-world driving simulations, each step is a testament to the complex engineering behind these small but vital parts. Moreover, the process involves the use of advanced brake pad materials, cutting-edge machinery, and years of accumulated expertise to achieve optimal performance, durability, and compliance with environmental regulations. Let’s dive into the intricate journey of how high-performance brake pads are brought to life, step by step.
1. Research and Development: The Foundation of Brake Pads
Every brake pad manufacturing process begins in the laboratory, where engineers work to create products that meet rigorous standards of performance, durability, and safety.
Material Formulation Design: Engineers meticulously balance the friction material development to achieve optimal wear resistance, noise reduction, and braking efficiency. This involves extensive experimentation with materials like carbon fibers, aramid fibers, and graphite to create a formula that ensures consistent performance under varying conditions.
Prototype Testing: Prototypes are tested on dynamometers, simulating real-world conditions like sudden braking, high speeds, and varying temperatures. These tests help engineers fine-tune the brake pad design for reliability and efficiency.

Performance Optimization: Advanced features such as chamfers, slots, and shims are added to improve noise, vibration, and harshness (NVH) characteristics. This stage often involves iterative refinements to strike the perfect balance between cost-effectiveness and functionality.
By the end of this phase, manufacturers have a robust blueprint for the production of brake pads that aligns with stringent industry standards.
2. Material Selection and Preprocessing: Ensuring High-Quality Inputs
High-quality brake pad materials are the cornerstone of reliable products. The selection and preprocessing of materials play a critical role in determining the final product's performance.
Rigorous Material Screening: Each batch of raw materials undergoes comprehensive testing for physical properties such as hardness, tensile strength, and abrasion resistance. Chemical properties, including ash content and heavy metal levels, are also analyzed to meet environmental and safety regulations, contributing to the creation of eco-friendly brake pads.

Preprocessing for Purity: Materials often contain impurities that could compromise performance. Preprocessing techniques such as washing, drying, and sieving remove these impurities, improving the material’s consistency and enhancing its physical attributes. This step ensures the raw materials are ready for the demanding brake pad manufacturing process that follows.
3. Formulation and Mold Design: Setting the Stage for Excellence
Once raw materials are prepared, the focus shifts to creating the perfect friction material formula and designing molds that ensure precision during manufacturing.
Custom Formulations: Each formulation is tailored to specific performance requirements, such as heavy-duty braking, quiet operation, or extended durability. Engineers carefully calculate the proportions of abrasives, binders, and fillers to achieve these goals.

Precision Mold Design: Molds are engineered to exact specifications, ensuring the brake pad's dimensions and features are consistent. The design process also takes into account factors like uniform material distribution and ease of removal after pressing, which are critical for maintaining high production efficiency.
This stage sets the foundation for the high-performance brake pads’ structural integrity and performance characteristics.
4. Manufacturing Process: Bringing Brake Pads to Life
The production of brake pads involves a series of highly coordinated steps to transform raw materials into finished products.
Steel Backing Plate Preparation: Steel plates are cut and stamped into the required shape, then treated to remove oils and impurities. A layer of adhesive is applied to ensure strong bonding with the friction material. This step is critical, as a weak bond could lead to brake pad failure.


Material Mixing and Forming: The raw materials are weighed according to the formula and mixed thoroughly to ensure uniformity. The mixture is then cold-pressed into a preliminary shape, ensuring precise dimensions and material density.

High-Pressure, High-Temperature Molding: The cold-pressed pad and steel backing plate are fused together under intense pressure and heat. This process, known as "one-step molding," ensures a durable bond and enhances the friction material’s strength.
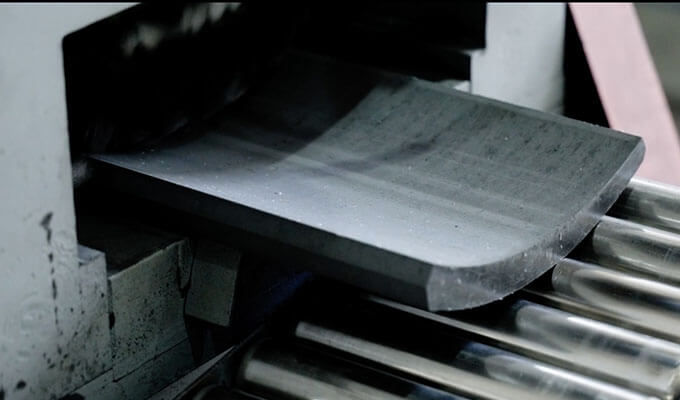
5. Finishing and Quality Control: Perfecting the Product
After the automotive brake pads are molded, they undergo various finishing processes to enhance functionality, appearance, and durability.
Heat Treatment: The pads are cured in ovens, where controlled heat solidifies the adhesive and strengthens the friction material. This step eliminates internal stresses and improves the pad’s resistance to high temperatures.
Surface Processing: The pads are ground, chamfered, and slotted using diamond tools. Chamfers and slots reduce noise and vibration, while precise grinding ensures a smooth, even surface for optimal contact with the rotor.

Anti-Corrosion Treatment: Non-friction surfaces are coated with protective layers of paint, powder coating, or electrostatic spray to prevent rust and enhance the product's aesthetic appeal.
Quality control is the final and most critical step. Random samples are tested for dimensions, density, chemical composition, and performance metrics like compression and heat resistance. Any deviations are flagged, and adjustments are made to maintain the highest standards of brake pad quality control.
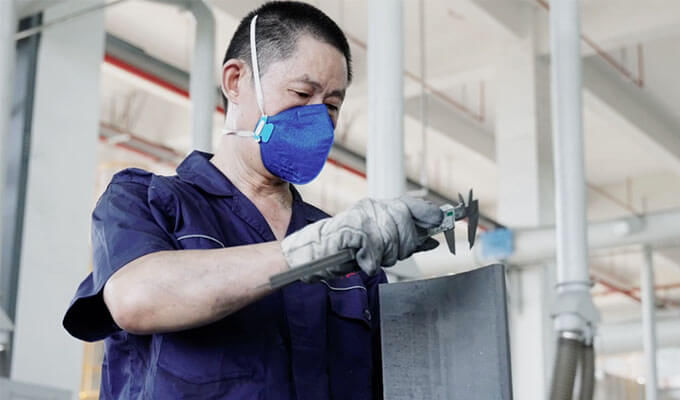
Automotive Packaging Process
The final step in the brake pads manufacturing process is the automotive packaging process, which plays a critical role in ensuring the product's quality, safety, and market readiness. Once brake pads pass quality control inspections, they are carefully packaged to protect them from damage during transportation and storage. Packaging typically involves placing the brake pads in protective sleeves or molded trays to prevent scratches or contamination. Each package is then sealed and labeled with essential information, including product specifications, part numbers, and usage instructions. High-quality packaging not only safeguards the brake pads but also enhances their professional presentation, reflecting the manufacturer's brand and commitment to excellence. For some manufacturers, this process includes eco-friendly initiatives, utilizing recyclable or biodegradable materials to align with sustainability goals.
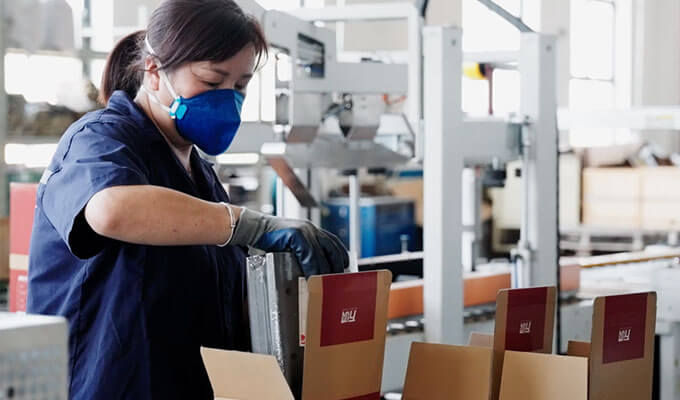
Driving Innovation in Brake Pad Manufacturing
The manufacturing process of brake pads is a blend of science, technology, and craftsmanship. Each stage, from friction material development to final testing, ensures that automotive brake pads meet the demands of modern vehicles. As the industry shifts toward sustainable practices and eco-friendly brake pads, manufacturers continue to innovate with advanced materials and methods. By understanding this process, vehicle manufacturers and repair companies can better appreciate the intricate efforts behind every high-performance brake pad that ensures safety on the road.

About us
Zhejiang Wanhong Auto Parts Co., Ltd., is a China leading brake pads and brake linings manufacturer with their brand Ultra Brake. Our cutting-edge manufacturing solutions are equipped with the latest technologies, including advanced automation systems for precision and consistency, ensuring superior product quality and efficiency in our brake pads and linings. Our advanced laboratory rigorously tests raw materials and finished products, supported by a senior engineering team dedicated to innovation and quality assurance. With a commitment to craftsmanship, we offer a diverse range of products, including heavy truck drums, bus discs, and passenger car disc brake brake pads and brake linings, all developed in-house. Our focus on custom manufacturing enables us to meet the unique needs of our clients while maintaining the highest industry standards.
CONTACT US
Zhejiang Wanhong Auto Parts Co., Ltd.
Email: info@ultra-brake.com
Tel: No.75, Changxing 1st Road, Xiping Street, Songyang County,
Lishui City, Zhejiang Province
Phone: +8615867107717
Comments